發(fā)動(dòng)機(jī)模擬系統(tǒng)及扭轉(zhuǎn)疲勞試驗(yàn)系統(tǒng)
聲明:您必須遵守我們的協(xié)議,如果您下載了該資源行為將被視為對(duì)《電天下賬號(hào)管理規(guī)范》全部?jī)?nèi)容的認(rèn)可,本網(wǎng)站資源來(lái)自原創(chuàng),僅供用于學(xué)習(xí)和交流,請(qǐng)勿用于商業(yè)用途。如有侵權(quán)、不妥之處,請(qǐng)舉報(bào)本資源,我們將及時(shí)審核處理!
發(fā)動(dòng)機(jī)模擬系統(tǒng)及扭轉(zhuǎn)疲勞試驗(yàn)系統(tǒng)
發(fā)動(dòng)機(jī)模擬系統(tǒng)及扭轉(zhuǎn)疲勞試驗(yàn)系統(tǒng)
BRTEAM公司成立于1954年,總部位于美國(guó)的西雅圖市。它在制造高性能震動(dòng)試驗(yàn)系統(tǒng)和扭轉(zhuǎn)疲勞試驗(yàn)方面有著豐富的經(jīng)驗(yàn)。TEAM的單軸向至多軸向電液伺服震動(dòng)臺(tái),涵蓋的頻率從零到1000Hz。它在全世界最早推出了6自由度震動(dòng)臺(tái)系統(tǒng)。獨(dú)特的設(shè)計(jì)和極高的工藝加工精度,使震動(dòng)臺(tái)系統(tǒng)有著極好的波形再現(xiàn)精度今天TEAM的電液伺服震動(dòng)臺(tái)產(chǎn)品擁有完整的系列,從單自由度到多自由度,從低頻到1000Hz的高頻TEAM公司也按照用戶的特殊要求,設(shè)計(jì)制造了許多匠心獨(dú)具的震動(dòng)臺(tái)實(shí)
文本預(yù)覽
Engine Simulator Reduces Development Time and Expense
John Davis
Team Corporation
Copyright ? 2002 Team Corporation
ABSTRACT
Traditionally development of engine-driven products has
required testing with an operating engine. Because an
operating engine is required, many tests are delayed until
operational engines are available for testing purposes.
Engines are frequently not available until very late in the
development process. Getting a late start on testing
naturally limits the amount of testing that can be
performed and the number of design alternatives that
can be evaluated.
Team Corporation’s 900 Series of Engine Simulation
Systems reduce development cost and time-to-market
for engine-driven systems and components. By providing
a programmable and flexible test platform, a Team
Engine Simulation Systems enables the development
engineer to perform more tests, more accurately, and
earlier in the development process. A typical Team Engine Simulation System with
integrated variable speed drive.
INTRODUCTION
By using data from similar engines or from CAE models,
The PC-based Engine Simulation Controller (ESSCON)
the Team ESS can be used at the very beginning of the
allows the operator to control the amplitude, frequency
engine development program to evaluate several design
and duration of vibration. In addition the speed of rotation
alternatives quickly. Results from these tests can be
can be controlled. A test scheduling feature allows for
used to narrow the alternatives to the most promising.
programming of engine duty cycles and looping of test
Subsequent testing that incorporates measured data
sequences.
obtained on prototype engines allows quick and reliable
comparison of the performance of the various designs
Aside from the physical space required, there are
under controlled, repeatable conditions.
numerous safety and environmental issues related to an
engine-drive testing facility. Among these are fuel
The Team ESS uses closed-loop vibration control to
handling, exhaust gas handling, and fire-suppression
provide repeatable test conditions test after test. By
systems. By eliminating the need for fuel and the
eliminating uncontrolled variables such as changes in
production of exhaust gases the Team ESS can
engine performance over time and variations from
significantly reduce facility costs. In addition, the flexibility
engine to engine, the Team ESS brings a higher level of
of the Team ESS further reduces the overall facility
confidence to the testing process.
investment.
\\Ntserver\sales\Data\Application Notes\Engine Simulator Reduces Development Time and Expense.doc Page 1 of 4SYSTEM DETAILS
Team Corporation offers ESS systems with dynamic
torque capabilities ranging from 1.1 to 4.5 kN-m at
frequencies up to 600 Hz and rotational speeds up to
10000 rpm. This wide range of capability allows Team to
provide ESS solutions for the full range of passenger car
and heavy truck applications.
A complete ESS is comprised of the following sub-
systems:
Variable Speed Drive (VSD) – The VSD provides rotary
motion and steady state torque for the engine simulation
system. Typically a variable speed DC drive, the VSD
may be integrated into the ESS (up to 75 kW). For higher
power requirements an external drive may be used.
Spinning Rotary Actuator (SRA) – The SRA is the
heart of the ESS. It provides the dynamic torsional
vibrations to the test specimen. The SRA can be
described as a rotary actuator whose housing is allowed
to rotate. All dynamic torque, acceleration and
displacement are generated relative to the actuator
housing. Any steady state torque produced by the VSD
also acts through the spinning rotary actuator.
A belt test setup on an early Team Engine Simulation
The primary working components of the spinning rotary
System.
actuator are the housing and the rotor. The housing is
driven by the VSD either directly or using a toothed belt.
The rotor maintains its position relative to the housing by
means of hydraulic pressure on the rotor’s vanes. Servovalve Assembly – The servovalve assembly is
Modulating the pressure on the rotor vanes produces comprised of a Team high-frequency voice coil driven
dynamic torque. pilot stage and a Team high-flow slave stage. Optimized
for high frequency response, the servovalve assembly
The SRA is supported by two hydrostatic bearings; one enables the ESS to operate at frequencies up to and
each at the front and rear of the SRA. Hydrostatic beyond 600 Hz.
bearings are used to minimize friction. The front bearing
of the actuator assembly also serves as a hydraulic slip Instrumentation and Control (ESSCON) – The
ring that allows oil to flow from the stationary servovalves instrumentation and control system controls and
into the actuator. monitors the test in progress and the operation of the
ESS. The primary control element is the angular
Attached to the housing are two disks. The larger of the acceleration of the rotor. This is measured by means of
two is an inertia disk that reacts the dynamic torque one or more standard linear accelerometer mounted
generated by the rotor. The inertia disk is sized so as to tangentially to the axis of rotation at a known, fixed
have an inertia that is many times greater than the inertia radius. Accelerometers are used for low cost, high
of the test load to maximize the energy transmitted to the resolution and the ability to operate at zero speed.
test load. The second disk is a brake disk. The brake is
used to automatically or manually stops the ESS in the The linear acceleration measured by the accelerometer
event of an emergency. is converted to angular units using a simple conversion
John Davis
Team Corporation
Copyright ? 2002 Team Corporation
ABSTRACT
Traditionally development of engine-driven products has
required testing with an operating engine. Because an
operating engine is required, many tests are delayed until
operational engines are available for testing purposes.
Engines are frequently not available until very late in the
development process. Getting a late start on testing
naturally limits the amount of testing that can be
performed and the number of design alternatives that
can be evaluated.
Team Corporation’s 900 Series of Engine Simulation
Systems reduce development cost and time-to-market
for engine-driven systems and components. By providing
a programmable and flexible test platform, a Team
Engine Simulation Systems enables the development
engineer to perform more tests, more accurately, and
earlier in the development process. A typical Team Engine Simulation System with
integrated variable speed drive.
INTRODUCTION
By using data from similar engines or from CAE models,
The PC-based Engine Simulation Controller (ESSCON)
the Team ESS can be used at the very beginning of the
allows the operator to control the amplitude, frequency
engine development program to evaluate several design
and duration of vibration. In addition the speed of rotation
alternatives quickly. Results from these tests can be
can be controlled. A test scheduling feature allows for
used to narrow the alternatives to the most promising.
programming of engine duty cycles and looping of test
Subsequent testing that incorporates measured data
sequences.
obtained on prototype engines allows quick and reliable
comparison of the performance of the various designs
Aside from the physical space required, there are
under controlled, repeatable conditions.
numerous safety and environmental issues related to an
engine-drive testing facility. Among these are fuel
The Team ESS uses closed-loop vibration control to
handling, exhaust gas handling, and fire-suppression
provide repeatable test conditions test after test. By
systems. By eliminating the need for fuel and the
eliminating uncontrolled variables such as changes in
production of exhaust gases the Team ESS can
engine performance over time and variations from
significantly reduce facility costs. In addition, the flexibility
engine to engine, the Team ESS brings a higher level of
of the Team ESS further reduces the overall facility
confidence to the testing process.
investment.
\\Ntserver\sales\Data\Application Notes\Engine Simulator Reduces Development Time and Expense.doc Page 1 of 4SYSTEM DETAILS
Team Corporation offers ESS systems with dynamic
torque capabilities ranging from 1.1 to 4.5 kN-m at
frequencies up to 600 Hz and rotational speeds up to
10000 rpm. This wide range of capability allows Team to
provide ESS solutions for the full range of passenger car
and heavy truck applications.
A complete ESS is comprised of the following sub-
systems:
Variable Speed Drive (VSD) – The VSD provides rotary
motion and steady state torque for the engine simulation
system. Typically a variable speed DC drive, the VSD
may be integrated into the ESS (up to 75 kW). For higher
power requirements an external drive may be used.
Spinning Rotary Actuator (SRA) – The SRA is the
heart of the ESS. It provides the dynamic torsional
vibrations to the test specimen. The SRA can be
described as a rotary actuator whose housing is allowed
to rotate. All dynamic torque, acceleration and
displacement are generated relative to the actuator
housing. Any steady state torque produced by the VSD
also acts through the spinning rotary actuator.
A belt test setup on an early Team Engine Simulation
The primary working components of the spinning rotary
System.
actuator are the housing and the rotor. The housing is
driven by the VSD either directly or using a toothed belt.
The rotor maintains its position relative to the housing by
means of hydraulic pressure on the rotor’s vanes. Servovalve Assembly – The servovalve assembly is
Modulating the pressure on the rotor vanes produces comprised of a Team high-frequency voice coil driven
dynamic torque. pilot stage and a Team high-flow slave stage. Optimized
for high frequency response, the servovalve assembly
The SRA is supported by two hydrostatic bearings; one enables the ESS to operate at frequencies up to and
each at the front and rear of the SRA. Hydrostatic beyond 600 Hz.
bearings are used to minimize friction. The front bearing
of the actuator assembly also serves as a hydraulic slip Instrumentation and Control (ESSCON) – The
ring that allows oil to flow from the stationary servovalves instrumentation and control system controls and
into the actuator. monitors the test in progress and the operation of the
ESS. The primary control element is the angular
Attached to the housing are two disks. The larger of the acceleration of the rotor. This is measured by means of
two is an inertia disk that reacts the dynamic torque one or more standard linear accelerometer mounted
generated by the rotor. The inertia disk is sized so as to tangentially to the axis of rotation at a known, fixed
have an inertia that is many times greater than the inertia radius. Accelerometers are used for low cost, high
of the test load to maximize the energy transmitted to the resolution and the ability to operate at zero speed.
test load. The second disk is a brake disk. The brake is
used to automatically or manually stops the ESS in the The linear acceleration measured by the accelerometer
event of an emergency. is converted to angular units using a simple conversion
發(fā)動(dòng)機(jī)模擬系統(tǒng)是一種高度精密的測(cè)試設(shè)備,用于在實(shí)驗(yàn)室條件下對(duì)汽車、航空航天或其它動(dòng)力機(jī)械的發(fā)動(dòng)機(jī)進(jìn)行仿真工作負(fù)載分析。它通過(guò)計(jì)算機(jī)控制,能夠精確地模仿真實(shí)發(fā)動(dòng)機(jī)在各種工況下的運(yùn)行狀態(tài),如不同轉(zhuǎn)速、扭矩、負(fù)荷以及溫度變化等,以便評(píng)估發(fā)動(dòng)機(jī)在實(shí)際使用中的性能、耐久性和效率。這種系統(tǒng)廣泛應(yīng)用于發(fā)動(dòng)機(jī)設(shè)計(jì)驗(yàn)證、優(yōu)化和改進(jìn)過(guò)程,以確保其在長(zhǎng)時(shí)間和極端條件下的可靠性和穩(wěn)定性。
而扭轉(zhuǎn)疲勞試驗(yàn)系統(tǒng)則是專門針對(duì)發(fā)動(dòng)機(jī)或其他旋轉(zhuǎn)部件(如傳動(dòng)軸、連桿、曲軸等)在承受重復(fù)扭轉(zhuǎn)載荷時(shí)的強(qiáng)度和壽命評(píng)估。該系統(tǒng)通常包括一個(gè)可調(diào)節(jié)扭力和旋轉(zhuǎn)速度的加載裝置,與一臺(tái)或多臺(tái)風(fēng)扇、電機(jī)或者液壓馬達(dá)配合,施加周期性或隨機(jī)的扭轉(zhuǎn)應(yīng)力到被試件上。通過(guò)對(duì)這些參數(shù)的精確控制和長(zhǎng)期監(jiān)測(cè),可以評(píng)估材料或結(jié)構(gòu)在反復(fù)扭轉(zhuǎn)作用下的裂紋擴(kuò)展、塑性變形乃至斷裂的風(fēng)險(xiǎn),從而為產(chǎn)品的可靠性和使用壽命提供科學(xué)依據(jù)。這兩個(gè)系統(tǒng)共同構(gòu)成了發(fā)動(dòng)機(jī)性能與耐久性研究的重要組成部分,在現(xiàn)代工程技術(shù)領(lǐng)域中占有重要地位。
發(fā)動(dòng)機(jī)模擬系統(tǒng)及扭轉(zhuǎn)疲勞試驗(yàn)系統(tǒng)的相關(guān)資源推薦
會(huì)員專享
會(huì)員限時(shí)八折,點(diǎn)擊立即查看
升級(jí)會(huì)員獲取海量資源免費(fèi)下載
會(huì)員免費(fèi)下載
5D幣 購(gòu)買
上傳資源賺收益
格式:pdf
瀏覽:215
收藏:0
瀏覽:215??|??
收藏:0
上傳時(shí)間:2009-12-12
大小:68.5K
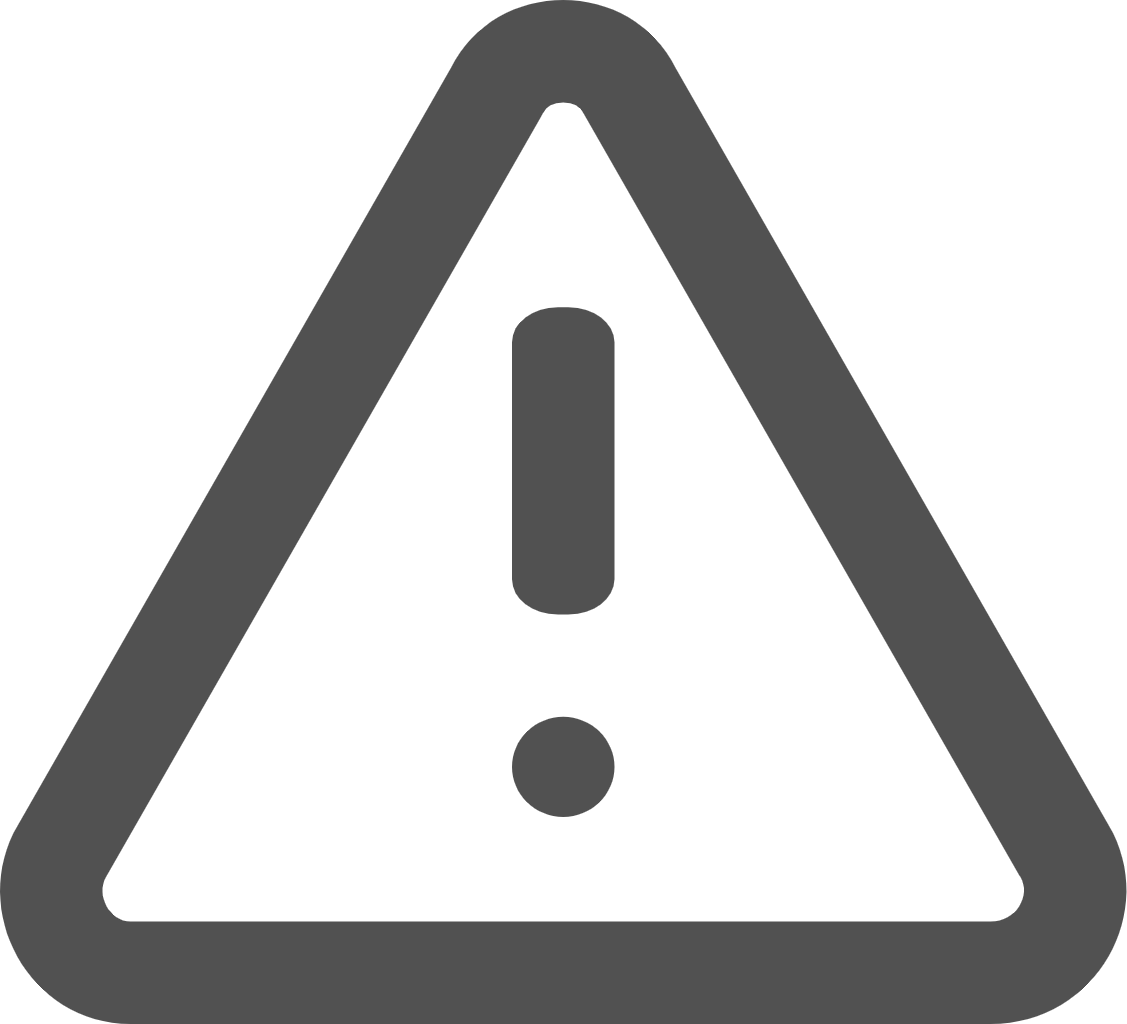
排名
昵稱
瓦特值